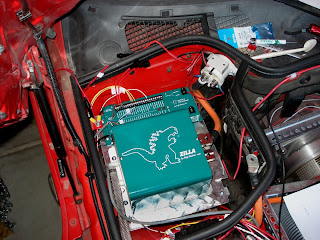
You may notice that I moved the main contactor (that white cylinder toward the top right corner of the frame). It had been located in the lower right frame, but it became clear that running the 2/0 cable to the controller with the contactor in the old position wasn't going to be very easy. I think it will work out much better in this location.
I also spent some time trying to figure out if I will be able to make the stock tachometer work with the Zilla. The Zilla can drive a standard tachometer for a 4 or 6 cylinder car. The problem I face is that the signal that was sent to this tachometer was clearly sent via the CAN bus in a format that I have no way of determining. The tachometer itself has 4 pins that plug into a circuit board right behind the instrument.
On a normal aftermarket tachometer, those four wires would be laid out like this:
1 - to the coil or alternator
2 - 12 volt positive
3 - chassis ground
4 - 12 volt for the instrument's light.
On the stock tach, I was able to measure one pin at 8.5 volts, a second at .56 volts and the other two had no voltage. Nor did they have continuity to ground. Uh huh. Well, it's likely that there was some sort of signal sent down one of those two wires that shows no voltage, but which wire, and what that signal was, I have no idea. It could have been a 12 volt pulse. It could have been a pulse that tied the instrument to ground. No way to tell. I'm likely going to have to replace it with an after market one. But before I do, I'll experiment with it a bit. I might get it to work, I might get it to send off some funny smelling blue smoke. Either way it will be fun.
Oh, and still no word on the batteries. Curses!